SAE/AISI 4340 Alloy Steel (UNS G43400)
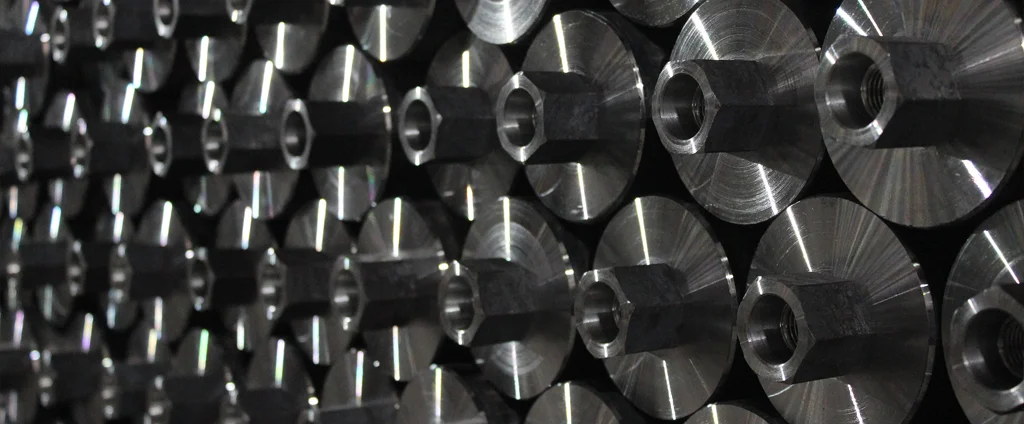
SAE/AISI 4340 alloy steel is a low-alloy, high-strength steel known for its outstanding toughness, fatigue resistance, and hardenability. Its mechanical and thermal properties make it highly suitable for critical applications in demanding industries such as aerospace, automotive, and oil and gas.
Chemical Composition | ||
---|---|---|
Element | Min | Max |
Iron | 95.19% | 96.33% |
Carbon | 0.37% | 0.43% |
Chromium | 0.70% | 0.90% |
Manganese | 0.60% | 0.80% |
Molybdenum | 0.20% | 0.30% |
Nickel | 1.65% | 2.00% |
Phosphorous | —— | 0.035% |
Silicon | 0.15% | 0.30% |
Sulfur | —— | 0.04% |
The following table provides a list of SAE/AISI 4340 properties in both SI and US customary/Imperial units.
Click on the button to switch between Metric and Imperial units.
Physical Properties | Metric |
---|---|
Density | 7850 kg/m3 |
Mechanical Properties | Metric |
Tensile Strength (Ultimate) | 745 MPa |
Tensile Strength (Yield) | 470 MPa |
Young’s Modulus (E) | 190 - 210 GPa |
Bulk Modulus (K) | 140 GPa |
Shear Modulus (G) | 80 GPa |
Elongation at Break | 22% |
Reduction of Area | 50% |
Poisson’s Ratio (ν) | 0.27 - 0.30 |
Brinell Hardness | 217 |
Thermal Properties | Metric |
Thermal Conductivity | 44.5 W/m·K |
Specific Heat Capacity (Cp) | 470 J/kg·K |
Coefficient of Thermal Expansion (αL) | 1.23×10-5 1/°C |
Electrical Properties | Metric |
Electrical Conductivity | 4.35×106 S/m |
Electrical Resistivity | 2.3×10-7 Ω·m |
The values in this table are approximate and can vary depending on various factors such as the specific manufacturing process and heat treatment applied to the alloy.
Advantages & Disadvantages of 4340 Alloy Steel
Advantages | Disadvantages |
---|---|
High strength and toughness | Relatively high cost |
Excellent fatigue resistance | Requires careful heat treatment |
Good wear resistance | Moderate weldability |
High hardenability and heat treatability | Susceptible to surface corrosion |
Versatile application range | Lower machinability compared to some steels |
Good impact resistance |
Applications of 4340 Alloy Steel
AISI 4340 steel finds applications in various industries due to its exceptional strength, toughness, and heat treatability. Key applications include:
- Aerospace: Components in aircraft and aerospace industry such as landing gear components, engine parts, structural parts, and gears.
- Automotive: Critical components in high-performance automobiles and racing vehicles, including crankshafts, connecting rods, gears, and axle shafts.
- Oil and Gas: Drill collars, mud motor components, shafts, gears, and other heavy-duty equipment used in drilling, exploration, and extraction operations.
- Power Generation: Turbine shafts, generator components, and other parts subjected to high temperatures, high loads, and cyclic stress in power plants.
- Marine: Shafts, propeller components, and other critical parts in marine applications that require high strength, toughness, and resistance to corrosion.
- Tool and Die Making: Tooling components such as punches, dies, and mold inserts that require high strength, wear resistance, and toughness.
- Heavy Machinery: Components in heavy machinery, such as gears, shafts, and structural parts that need to withstand heavy loads and demanding operating conditions.
- Defense and Military: Various components in military vehicles, weapons systems, and aircraft, including gears, shafts, and structural parts.
- Mining and Construction: Components used in mining equipment, construction machinery, and earth-moving equipment that require high strength, durability, and resistance to wear.