SAE/AISI E4340 Alloy Steel (UNS G43406)
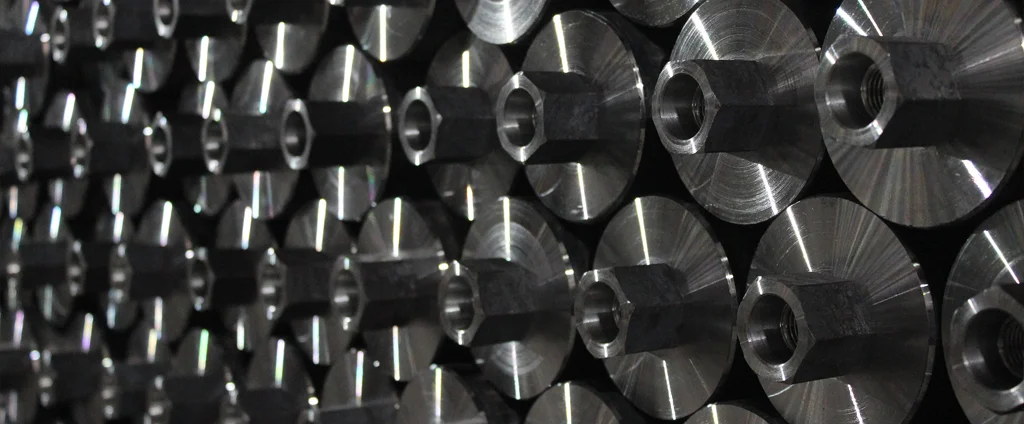
SAE/AISI E4340 steel is a medium-carbon, low-alloy grade recognized for its superior toughness, high strength, and excellent wear resistance. Commonly utilized in structural and high-stress applications, it is especially valued in aerospace, automotive, and industrial sectors for components requiring durability and reliability under demanding conditions.
Chemical Composition | ||
---|---|---|
Element | Min | Max |
Iron | 95.17% | 96.27% |
Carbon | 0.38% | 0.43% |
Chromium | 0.70% | 0.90% |
Manganese | 0.65% | 0.85% |
Molybdenum | 0.20% | 0.30% |
Nickel | 1.65% | 2.00% |
Phosphorous | —— | 0.025% |
Silicon | 0.15% | 0.30% |
Sulfur | —— | 0.02% |
The following table provides a list of SAE/AISI E4340 properties in both SI and US customary/Imperial units.
Click on the button to switch between Metric and Imperial units.
Physical Properties | Metric |
---|---|
Density | 7850 kg/m3 |
Mechanical Properties | Metric |
Tensile Strength (Ultimate) | 745 MPa |
Tensile Strength (Yield) | 470 MPa |
Young’s Modulus (E) | 190 - 210 GPa |
Bulk Modulus (K) | 140 GPa |
Shear Modulus (G) | 80 GPa |
Elongation at Break | 22% |
Reduction of Area | 50% |
Poisson’s Ratio (ν) | 0.27 - 0.30 |
Brinell Hardness | 217 |
Thermal Properties | Metric |
Thermal Conductivity | 44.5 W/m·K |
Specific Heat Capacity (Cp) | 470 J/kg·K |
Coefficient of Thermal Expansion (αL) | 1.13×10-5 1/°C |
Electrical Properties | Metric |
Electrical Resistivity | 2.48×10-7 Ω·m |
The values in this table are approximate and can vary depending on various factors such as the specific manufacturing process and heat treatment applied to the alloy.
Advantages & Disadvantages of E4340 Alloy Steel
Advantages | Disadvantages |
---|---|
High strength and toughness | Relatively high cost compared to carbon steels |
Excellent wear resistance | Requires careful heat treatment for best results |
Good hardenability | Prone to distortion during heat treatment |
High fatigue resistance | Limited weldability |
Good impact resistance | Susceptible to cracking if improperly heat treated |
Wide range of heat treatment options | Requires skilled machining for complex shapes |
Applications of E4340 Alloy Steel
AISI E4340 alloy steel is extensively employed across diverse industries requiring high strength, toughness, and wear resistance, including:
- Aerospace Components: Used in manufacturing critical parts such as gears, shafts, landing gear components, structural elements, and engine parts.
- Automotive and Racing Components: Utilized for high-performance, durable parts including crankshafts, connecting rods, gears, camshafts, and other high-stress engine components, withstanding extreme loads and vibrations.
- Oil and Gas Industry: Applied in drill collars, drill string components, gears, and shafts for downhole tools and equipment, offering toughness and deformation resistance in harsh environments.
- Power Transmission: Manufactured into gears, shafts, and other parts for heavy machinery, gearboxes, and power generation equipment, ensuring efficient power transfer and durability.
- Tool and Die Making: Selected for punches, dies, forging dies, and tooling components subject to high loads and repeated impacts due to its high strength and toughness.