SAE/AISI 8625 Alloy Steel (UNS G86250)
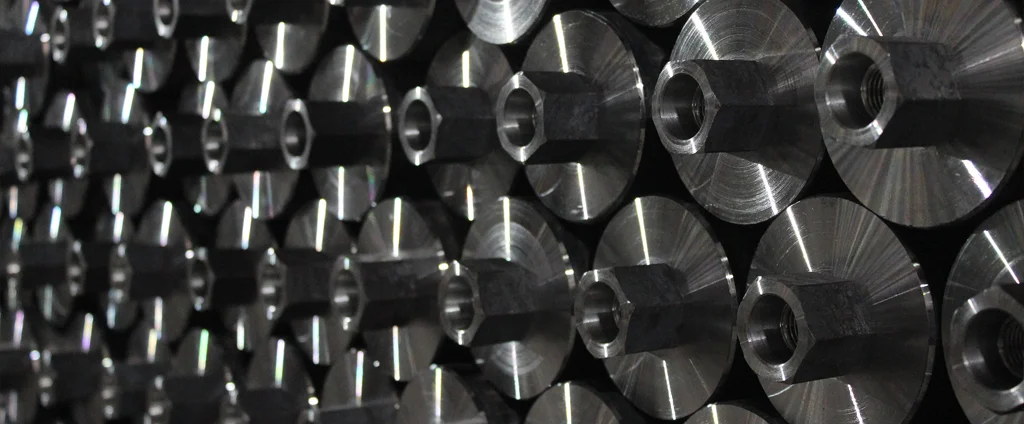
SAE/AISI 8625 is a low-alloy, nickel-chromium-molybdenum steel known for its superior strength, toughness, and wear resistance. Commonly used in aerospace, automotive, and heavy machinery industries, it offers excellent hardenability and performance under stress, making it a reliable choice for high-load structural components and mechanical systems.
Chemical Composition | ||
---|---|---|
Element | Min | Max |
Iron | 96.89% | 97.97% |
Carbon | 0.23% | 0.28% |
Chromium | 0.40% | 0.60% |
Manganese | 0.70% | 0.90% |
Molybdenum | 0.15% | 0.25% |
Nickel | 0.40% | 0.70% |
Phosphorous | —— | 0.035% |
Silicon | 0.15% | 0.30% |
Sulfur | —— | 0.04% |
The following table provides a list of SAE/AISI 8625 properties in both SI and US customary/Imperial units.
Click on the button to switch between Metric and Imperial units.
Physical Properties | Metric |
---|---|
Density | 7850 kg/m3 |
Mechanical Properties | Metric |
Young’s Modulus (E) | 190 - 210 GPa |
Bulk Modulus (K) | 140 GPa |
Shear Modulus (G) | 80 GPa |
Poisson’s Ratio (ν) | 0.27 - 0.30 |
Brinell Hardness | 179 - 223 |
Thermal Properties | Metric |
Thermal Conductivity | 46.6 W/m·K |
Specific Heat Capacity (Cp) | 470 J/kg·K |
Electrical Properties | Metric |
Electrical Conductivity | 4.23×106 S/m |
Electrical Resistivity | 2.36×10-7 Ω·m |
The values in this table are approximate and can vary depending on various factors such as the specific manufacturing process and heat treatment applied to the alloy.
Advantages & Disadvantages of 8625 Alloy Steel
Advantages | Disadvantages |
---|---|
High strength and toughness | Relatively high cost compared to carbon steels |
Good hardenability | Requires specialized heat treatment for optimal performance |
Excellent wear resistance when carburized | Susceptible to surface cracking during quenching |
Suitable for high-load applications | Limited availability in certain regions |
Good machinability when properly heat treated | Requires careful handling and maintenance to prevent corrosion |
Offers good fatigue resistance | Moderate weldability, may require preheating and post-weld heat treatment |
Applications of 8625 Alloy Steel
SAE/AISI 8625 is widely used across industries requiring components with high strength, durability, and wear resistance, including:
- Gears and Gear Shafts: Its excellent combination of strength and toughness makes it suitable for use in gear systems, especially in high-load applications where wear resistance is crucial.
- Shafts and Axles: The high strength and good machinability make it a preferred choice for shafts and axles subjected to heavy loads and stress. These components are commonly found in automotive, machinery, and equipment industries.
- Sprockets and Camshafts: The wear resistance, particularly when carburized, makes it an ideal material for sprockets and camshafts that require prolonged use without significant wear or deformation.
- Bearings: Good hardenability and fatigue resistance make it suitable for manufacturing anti-friction bearings, providing durability and reliable performance in demanding rotating applications.
- Automotive Components: Its strength, toughness, and wear resistance make it applicable for various automotive components, including crankshafts, connecting rods, transmission parts, and differential gears.
- Heavy Machinery Parts: Used in the manufacturing of heavy machinery parts like drive shafts, couplings, and structural components that require high strength and resistance to wear and fatigue.
- Tooling and Dies: Due to its toughness and wear resistance, it is employed in tooling and die applications, such as punches, dies, and molds, where high durability and precision are essential.
- Mechanical Components: Utilized in a wide range of mechanical components that require a balance of strength, toughness, and wear resistance, such as gears, shafts, couplings, and springs.