Aluminum Alloy 7050 (UNS A97050)
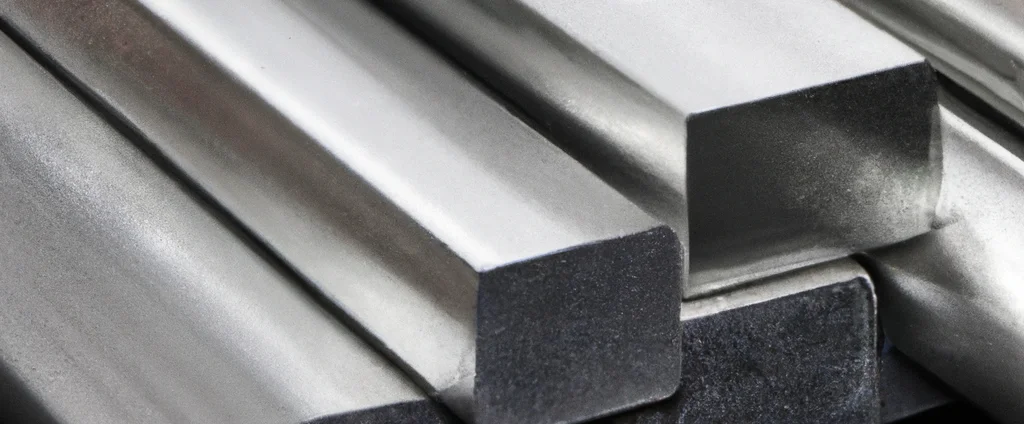
Aluminum 7050 is a high-strength aluminum alloy commonly used in the aerospace industry for structural components, such as aircraft fuselage and wing structures. It is known for its excellent strength-to-weight ratio and good resistance to fatigue.
Chemical Composition | ||
---|---|---|
Element | Min | Max |
Aluminum | 87.3% | 92.1% |
Chromium | —— | 0.04% |
Copper | 2.0% | 2.6% |
Iron | —— | 0.15% |
Magnesium | 1.9% | 2.6% |
Manganese | —— | 0.1% |
Silicon | —— | 0.12% |
Titanium | —— | 0.06% |
Zinc | 5.7% | 6.7% |
Zirconium | 0.08% | 0.15% |
Residuals | —— | 0.15% |
The following table provides a list of aluminum 7050 properties in both SI and US customary/Imperial units.
Click on the button to switch between Metric and Imperial units.
Physical Properties | Metric |
---|---|
Density | 2600 - 2800 kg/m3 |
Mechanical Properties | Metric |
Tensile Strength | 490 - 570 MPa |
Yield Strength | 390 - 500 MPa |
Shear Strength | 280 - 330 MPa |
Fatigue Strength | 150 - 240 MPa |
Young’s Modulus (E) | 70 - 80 GPa |
Shear Modulus (G) | 26 GPa |
Elongation at Break | 11% |
Poisson’s Ratio (ν) | 0.33 |
Thermal Properties | Metric |
Melting Point | 494 °C |
Thermal Conductivity | 180 W/m·K |
Specific Heat Capacity (Cp) | 860 J/kg·K |
Coefficient of Thermal Expansion (αL) | 2.4×10-5 1/°C |
Electrical Properties | Metric |
Electrical Conductivity | 2.35×107 S/m |
Electrical Resistivity | 4.3×10-8 Ω·m |
The values in this table are approximate and can vary depending on various factors such as the specific manufacturing process and heat treatment applied to the alloy.
Advantages & Disadvantages of Aluminum 7050
Advantages | Disadvantages |
---|---|
High strength-to-weight ratio | High cost |
Fatigue resistance | Susceptibility to corrosion |
Machinability | Limited formability |
Heat treatable | Weldability |
Applications of Aluminum 7050
Aluminum 7050 is the benchmark alloy for industries demanding uncompromising strength, lightweight performance, and fatigue resistance. Key applications include:
- Aerospace Structures: Extensively utilized in aerospace applications, including aircraft structures, fuselage frames, wing spars, and wing skins. The high strength-to-weight ratio and excellent fatigue resistance make it ideal for reducing weight while maintaining structural integrity.
- Defense and Military Equipment: Employed in the defense industry for the production of military aircraft components, missile structures, and armored vehicles. The strength, durability, and resistance to stress corrosion cracking make it suitable for demanding defense applications.
- Sporting Goods: Used in the manufacturing of sporting goods such as bicycle frames, handlebars, and components. The high strength and light weight contribute to improved performance and maneuverability in various sports.
- Marine Components: Due to excellent corrosion resistance and high strength, it’s utilized in marine applications including boat hulls, masts, and other structural parts that require both durability and weight savings.
- Automotive Industry: Finds use in the automotive sector for lightweight structural components, suspension systems, and chassis parts. The strength and stiffness properties contribute to fuel efficiency, performance, and overall vehicle weight reduction.
- High-Performance Machinery: Employed in the production of high-performance machinery, such as industrial equipment, machine frames, and components that require strength and durability under heavy loads.
- Robotics and Automation: Suitable for applications that require lightweight yet robust structures, such as robotic arms, automation frames, and support structures.