Chromium Copper (UNS C18200)
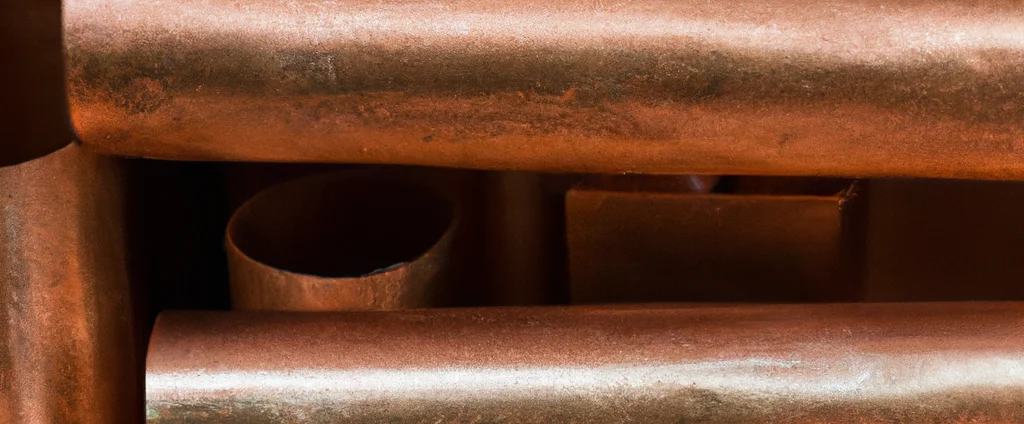
Chromium copper C18200 is a precipitation-hardened copper alloy known for its exceptional electrical conductivity, high strength, and thermal stability. It is widely used in electrical connectors, welding electrodes, and heat sinks.
Chemical Composition | ||
---|---|---|
Element | Min | Max |
Copper | 98.0% | 99.4% |
Chromium | 0.6% | 1.2% |
Iron | —— | 0.1% |
Lead | —— | 0.05% |
Silicon | —— | 0.1% |
Residuals | —— | 0.5% |
The following table provides a list of copper C18200 properties in both SI and US customary/Imperial units.
Click on the button to switch between Metric and Imperial units.
Physical Properties | Metric |
---|---|
Density | 8890 kg/m3 |
Mechanical Properties | Metric |
Tensile Strength (Ultimate) | 310 - 530 MPa |
Tensile Strength (Yield) | 100 - 450 MPa |
Shear Strength | 210 - 320 MPa |
Young’s Modulus (E) | 117 GPa |
Shear Modulus (G) | 50 GPa |
Elongation at Break | 10 - 40% |
Poisson’s Ratio (ν) | 0.3 |
Thermal Properties | Metric |
Melting Point | 1070 °C |
Thermal Conductivity | 320 W/m·K |
Specific Heat Capacity (Cp) | 385 J/kg·K |
Coefficient of Thermal Expansion (αL) | 1.76×10-5 1/°C |
Electrical Properties | Metric |
Electrical Conductivity | 4.64×107 S/m |
Electrical Resistivity | 2.2×10-8 Ω·m |
The values in this table are approximate and can vary depending on various factors such as the specific manufacturing process and heat treatment applied to the alloy.
Advantages & Disadvantages of Copper C18200
Advantages | Disadvantages |
---|---|
Electrical conductivity | High cost |
Thermal conductivity | Limited availability |
Corrosion resistance | Lower ductility |
High strength and hardness |
Applications of Copper C18200
Copper C18200 finds applications in various industries and sectors where its combination of high conductivity, strength, and corrosion resistance is advantageous. Key applications include:
- Electrical connectors and terminals: Widely used in electrical connectors, terminals, and conductive components where high electrical conductivity is essential. Its excellent conductivity allows for efficient transmission of electrical signals and power.
- Resistance welding electrodes: The high strength and thermal conductivity make it suitable for resistance welding electrodes. It can withstand the high heat generated during the welding process and efficiently dissipate heat, ensuring consistent and reliable welds.
- Switches and electrical contacts: Employed in switches and electrical contact components that require good conductivity, durability, and resistance to corrosion. This ensures reliable electrical performance and longevity in demanding environments.
- Heat sinks and heat exchangers: The high thermal conductivity makes it suitable for heat sinks and heat exchangers, as it efficiently transfers heat away from electronic components, helping to dissipate and regulate temperature effectively.
- Injection mold cores and cavities: The combination of strength and high thermal conductivity makes this alloy suitable for use in injection mold cores and cavities. It helps to cool and solidify the molten plastic efficiently, allowing for faster production cycles and improved part quality.
- Welding and brazing fixtures: The hardness and strength make it suitable for welding and brazing fixtures, as it can withstand the mechanical stresses and high temperatures associated with these processes, providing stability and reliability.
- Power transmission components: Used in power transmission components such as bus bars, current-carrying conductors, and transformer windings. The high conductivity ensures efficient power transfer and minimizes energy losses.
- Electronic components: Utilized in various electronic components, including connectors, printed circuit boards (PCBs), and semiconductor packages. Its conductivity and corrosion resistance are crucial for reliable electronic performance.