Nickel Aluminum Bronze (UNS C95800)
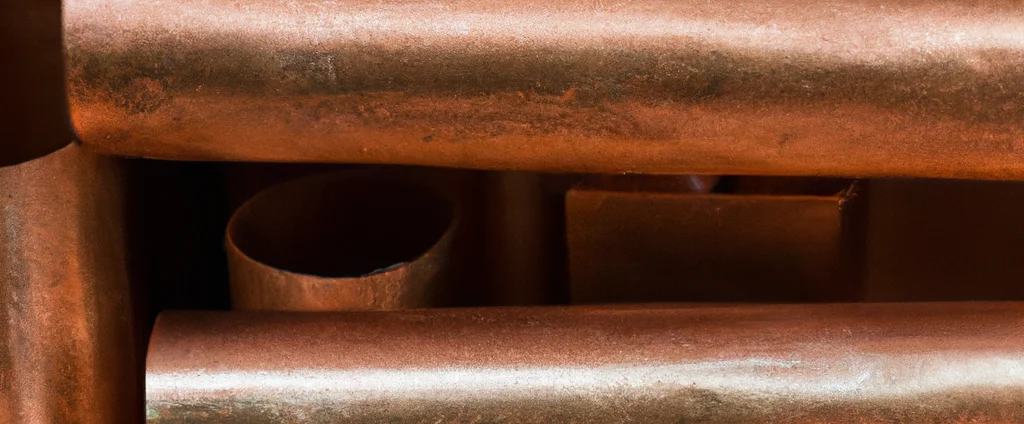
Nickel Aluminum Bronze C95800 is a premium copper alloy renowned for its exceptional corrosion resistance (especially in seawater), high strength, and wear resistance. It is widely used in marine, offshore, and industrial applications.
Chemical Composition | ||
---|---|---|
Element | Min | Max |
Copper | 79.0% | —— |
Aluminum | 8.5% | 9.5% |
Iron | 3.5% | 4.5% |
Lead | —— | 0.03% |
Manganese | 0.8% | 1.5% |
Nickel | 4.0% | 5.0% |
Silicon | —— | 0.1% |
The following table provides a list of bronze C95800 properties in both SI and US customary/Imperial units.
Click on the button to switch between Metric and Imperial units.
Physical Properties | Metric |
---|---|
Density | 7640 kg/m3 |
Mechanical Properties | Metric |
Tensile Strength (Ultimate) | 580 - 660 MPa |
Tensile Strength (Yield) | 240 - 360 MPa |
Young’s Modulus (E) | 110 GPa |
Shear Modulus (G) | 42 GPa |
Elongation at Break | 15 - 25% |
Poisson’s Ratio (ν) | 0.32 |
Brinell Hardness | 159 |
Rockwell Hardness (B) | 84 - 89 |
Thermal Properties | Metric |
Melting Point | 1045 - 1060 °C |
Thermal Conductivity | 36 W/m·K |
Specific Heat Capacity (Cp) | 440 J/kg·K |
Coefficient of Thermal Expansion (αL) | 1.62×10-5 1/°C |
Electrical Properties | Metric |
Electrical Conductivity | 4.06×106 S/m |
Electrical Resistivity | 2.43×10-7 Ω·m |
Magnetic Permeability | 1.05 |
The values in this table are approximate and can vary depending on various factors such as the specific manufacturing process and heat treatment applied to the alloy.
Advantages & Disadvantages of Nickel Aluminum Bronze C95800
Advantages | Disadvantages |
---|---|
Excellent corrosion resistance | High cost |
High strength | Limited availability |
Good wear and abrasion resistance | Weldability challenges |
Good machinability |
Applications of Nickel Aluminum Bronze C95800
Nickel Aluminum Bronze C95800 finds applications in various industries due to its desirable properties. Key applications include:
- Marine Industry: Widely used in this industry due to its excellent corrosion resistance in seawater and marine environments. It is employed in the construction of ship fittings, propellers, rudders, and seawater intake screens.
- Offshore Industry: Utilized for components subjected to harsh offshore conditions. It is used in equipment such as pumps, valves, connectors, and underwater fasteners, where corrosion resistance and high strength are crucial.
- Oil and Gas Industry: Employed for applications such as valves, pump components, and connectors. It can withstand the corrosive effects of hydrocarbons, brines, and other fluids encountered in oil and gas production.
- Industrial Equipment: The high strength and wear resistance make it suitable for industrial applications. It is used in bushings, bearings, gears, and wear plates that are exposed to heavy loads, high pressures, and abrasive conditions.
- Aerospace Industry: Used in components such as landing gear bushings, thrust bearings, and valve guides. Its combination of strength, wear resistance, and corrosion resistance is advantageous in aerospace applications.
- Chemical Processing: The corrosion resistance makes it suitable for chemical processing equipment. It is used in pumps, valves, and fittings that handle corrosive chemicals, acids, and alkalis.